STEP FOUR: SECOND STAGE BINDER REMOVAL AND SINTERING
In this process, which is performed in the highly controlled atmosphere of either a batch furnace or a continuous furnace, the brown part is staged on a ceramic or graphite “setter” and is then subjected to a precisely monitored temperature profile that gradually increases to approximately 85% of the metal’s melting temperature. The remaining binder is removed in the early part of this sintering cycle, followed by the elimination of pores and the fusing of the metal particles as the part shrinks isotropically to its design dimensions and transforms into a dense solid.
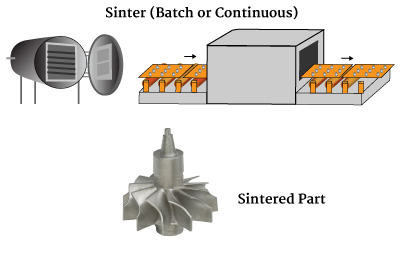
Sintering is commonly done either at a temperature which is slightly below the liquidus/solidus temperature of the alloy, or slightly above the liquidus temperature of the alloy. This is called solid-state sintering or liquid-state sintering respectively, which is either the part’s solidus temperature which is nearly high enough to induce partial melting in a process termed liquid-phase sintering. For example, a stainless-steel part might be heated to 1,350 to 1,400 degrees Celsius. Diffusion rates are high leading to high shrinkage (typically 18%–22%, binder volume dependent) and densification. If performed in a controlled atmosphere, it is common to reach 96%–99% of the theoretical density. The end-product metal has mechanical and physical properties similar to annealed parts made using conventional metalworking methods.
The end result is a net-shape or near-net-shape metal component, with properties similar to those of one machined from bar stock. When necessary, secondary operations such as coining, machining, heat treating, coating, and others, may be performed on the part to achieve tighter tolerances or enhanced properties.